Ergonomics of Material handling equipment, Design, Miscellaneous equipment
Sakshi Education
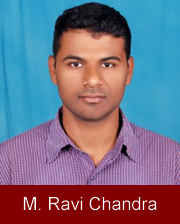
Ergonomics: The branch of engineering science in which biological science is used to study the relation between workers and their environments.
The word ‘Ergonomics’ has originated from Greek words Ergon meaning laws. So it is the study of the man in relation to his work. In USA and other countries it is called as ‘human engineering or human factors engineering’. ILO defines human engineering as, “The application of human biological sciences along with engineering sciences to achieve optimum mutual adjustment of men and his work, the benefits being measured in terms of human efficiency and well-being.”
The human factors or human engineering deals with man-machine system. Thus another definition highlighting the man-machine system is: “The design of human tasks, man- machine system, and effective accomplishment of the job, including displays for presenting information to human sensors, controls for human operations and complex man-machine systems.”
Human engineering emphasises on human beings and their interaction with products, equipment facilities and environment used in the work. Human engineering pursues to change the things people use and the environment in which they use the things to match in a better way the capabilities, limitations and needs of people.
“Ergonomics is the science of studying people at work and then designing tasks, jobs, information, tools, equipment, facilities and the working environment so people can be safe and healthy, effective, productive and comfortable.”
Human engineering (ergonomics) has two broader objectives:
Prioritize task analysis
Once we know material flow, it is time to evaluate tasks. This should be done on aimportance basis, first investigating the worst and most strenuous tasks. The safety and health unit should review accident statistics to determine priorities. The personnel who perform the tasks being evaluated are a vital source of information. Ask employees for their views on where the most vigorous, demanding and dangerous materials handling tasks exist likewise the poll supervisors and other management personnel. This is the time to examine the accident-investigation procedure to see if it is effective.
2.5 Analyse the job — tasks
Once the priorities have been set, break the tasks down into elements, which are the basic single actions needed to define the procedure at a particular stage of an operation. Among the considerations are:
Lessen reach requirements. Design the operation to house the smallest person‘s reach. Avoid needless material stacking, storing or placement for work-in-process material (such as neatly orienting parts in containers when they will be dumped out in the next operation). Structure the equipment to use gravity to move materials wherever achievable. Simplify tasks by combining operations and steps.
2.6 Analyse the job — load
The load consists of the item or collection of items handled, many of which are stored in containers.
Adjust all containers for the required sizes. Use large containers for high-flow volume and small containers for low capacity. Avoid using large containers for low-volume materials to reduce the need for workers to reach.
Remove handling hesitations. Remove an employee‘s doubt about whether he or she should manually or mechanically handle an object by using obviously small and large containers or parts. The plot for incoming materials to arrive in suitable containers minimizes product handling.
Ask clients how you can best design product-needs packaging to meet their materials supervision needs.
Reduce deadweight ratio of containers. Consider the weight of the container which must be frequently handled and transferred vs. the parts inside. The weight of the container should be least compared to the weight of the product. Keep physically handled loads as small as possible, paying consideration to the width and length. To prevent blocked vision, load height should be 30 inches or less when manually carried.
The load centre of gravity (or balancing point) should be as close as possible to the person handling it. Stress on the back increases as the distance from your centre of gravity increases. For example, a 10-pound dictionary held 30 inches away from the body‘s centre of gravity would be the equivalent of a compact 50-pound load held close to the body.
Ensure that the load will be easy to grip. This can be done by ordering cardboard boxes with handle cut-outs; using ampoules with handles, lift straps or textured containers; and avoiding awkwardly designed items. Stabilize contents in boxes and containers to reduce surprises. Insert vertical baffles or dividers, balancing the weight in a box or using packing materials to avoid shifting parts. Minimize the potential for injury by caring the employee from loads with sharp edges or projections. Potential for injury also exists with reactive loads, such as metal shavings.
2.7 Equipment
Consider the use of mechanical aids whenever possible to assist employees in their materials-handling needs. Examples include:
This includes, but is not limited to, identifying:
Bring only sufficient material to complete the job in the immediate work area. Extra material will either need extra handling to get it back to storage or will create overcrowding. Likewise, too little will require extra handling.
Consider the following, whenever possible, in jobs with considerable manual materials handling:
2.8 Environment
Review work areas for proper lighting levels. Poor lighting can cause accidents and injuries, and lessen quality of products.
Make allowances for weather situations including the following:
2.9 Recommend, review and implement changes
Once workers, staff and line employees have identified problems, they must be operated upon. At this point, shortages have been identified with possible answers in mind. The process is broken down into the following stages:
Two key elements of the review process are determining the influence proposed changes will have on other jobs, and what new difficulties will arise as a consequence of the changes made. Failure to consider these elements can result in a loss of credibility for the newly highlighted materials handling process.
3. Material Handling Ergonomics for human-beings
3.1 Lifting Principles
Maintain a neutral spine, keep your back straight!
Hold your abdominal muscles tight, but don’t hold your breath!
Use your legs to lift, not your back
Don’t bend over to lift
No twisting- move your feet instead
Maintain the load as close to your body as possible
3.2 Lifting Assistance
Seek assistance when lifting:
The word ‘Ergonomics’ has originated from Greek words Ergon meaning laws. So it is the study of the man in relation to his work. In USA and other countries it is called as ‘human engineering or human factors engineering’. ILO defines human engineering as, “The application of human biological sciences along with engineering sciences to achieve optimum mutual adjustment of men and his work, the benefits being measured in terms of human efficiency and well-being.”
The human factors or human engineering deals with man-machine system. Thus another definition highlighting the man-machine system is: “The design of human tasks, man- machine system, and effective accomplishment of the job, including displays for presenting information to human sensors, controls for human operations and complex man-machine systems.”
Human engineering emphasises on human beings and their interaction with products, equipment facilities and environment used in the work. Human engineering pursues to change the things people use and the environment in which they use the things to match in a better way the capabilities, limitations and needs of people.
“Ergonomics is the science of studying people at work and then designing tasks, jobs, information, tools, equipment, facilities and the working environment so people can be safe and healthy, effective, productive and comfortable.”
Human engineering (ergonomics) has two broader objectives:
- To improve the efficiency and effectiveness with which the activities (work) are carried out, so as to increase the ease of use, reduced errors and increase in productivity.
- To boost certain desirable human values including safety reduced stress and fatigue and improved quality of life.
Thus, in general the scope and function of ergonomics is “designing for human use and optimizing working and living conditions”. Thus human factors (ergonomics) learn and apply information about human behaviour. Abilities and restrictions and other characteristics to the design of tools, machines, systems, tasks, works and environment for productive, safe, comfortable and effective human use. Ergonomics aims at providing ease and improved working conditions so as to channelize the energy, skills of the workers into profitable productive work. This accounts for increased productivity, safety and decreases the fatigue. This helps to increase the plant utilization.
2 Elements of a Material Handling Ergonomics Program
2.1 Analyse management operations
We must first identify those materials handling is often one of the largest cost constituents of a product, operation or service. Needless handling of materials costs time and money.
We must understand the connection between workstation design and the works, that workers are expected to complete. The People responsible for planning work methods must pay particular consideration to details of the task involved to ensure the greatest possible synchronisation between the work method and the worker.
Make purchasing managers an important part of the materials handling program. Have them pay attention to details, such as size, weight, packaging and ease for handling. Use sold to/ship to arrangements to exclude in-plant handling wherever possible. Products being sent to your company for distribution may be more efficiently conveyed from your supplier to the customer, saving freight and handling. Reduce overall work-in-process quantities. Failure to do so often result in excess problems— extra handling, use of larger containers or parts piled. Housekeeping problems may grow, increasing possibilities of materials handling vehicle mishaps and damage to materials and completed goods. To reduce work-inprocess quantities, it is necessary to tighten up controls and shorten estimating for inventory, scheduling, ordering and shipping. Manufacturing products on an as ordered basis, instead of storing for anticipated use.
Perform product study. Alterations in the product sometimes result in decreased materials handling. Consider assuaging the product, and allowing a worker or conveyor to handle more pieces at one time. Plan to expand or change. Production usually suffers under packed conditions. Much of this material is reliant upon administration‘s policies and processes.
But even in the absence of management analysis, you personally can analyse and implement change in the following ways. Establish discarding and storage methods, and ways to progress material flow for scrap, waste materials, containers, tools and equipment. Each workstation must be analysed.
2.2 Material flow
It is usually not enough to simply observe and study a specific manual materials handling task. The key questions arise with respect to how the material is routed through the facility or work site that can only be answered by looking at the bigger picture.
Eliminate unnecessary materials handling by combining operations or shortening the distances that the materials must be moved. Look for crossing paths, loops, backtracking and a lack of direction during production. One benefit of short distances is the ability to link workstations by conveyors and reduce carrying distances. Also, less mechanical handling can mean fewer opportunities for forklift accidents. Walk through your operations with an employee. Make immediate simple changes. (Make written suggestions for observed cost-saving and people-saving changes that need approval or further evaluation.)
Take back to first principles, rearrange or change the process. Often, processes that are handled otherwise can be performed in a similar fashion to simplify the material flow. Plan an adequate aisleways for intended material flow, and emergency access and exit.
Employees must be able to evacuate quickly in an emergency. Small aisleways may restrict exits and cause panic. Emergency vehicles also must be able to quickly gain entrance. Adequate aisleways and exits facilitate the orderly movement of materials. Avoid the necessity of working in aisleways.
2.3 Workplace
Check the floor surfaces, repair flaws, depressions, holes, spoiled flooring and surfaces. Starting forces for carts can double or triple on poor surfaces. Worn-out or damaged wheels also can increase the required force. Insist on good housekeeping. Keep floor surfaces clean. Water, oil, grease and material scrap reduce traction and increase the force required to push or pull carts. Poor housekeeping only increases materials handling obstacles. Review plant design to remove building obstructions that interfere with materials handling.
In materials handling, “what goes down must come up.” To avoid repeated stooping and twisting, the goal is to bring both incoming and outgoing materials at each process to a suitable work height. We recommend at least a minimum of 20 inches above the floor, but ideally to knuckle height of about 30 inches. Reduce the need to raise or lower materials from above shoulder height. If you must raise or lower materials above shoulder height, store lighter objects on top shelves.
Remove constraints that prevent materials from being positioned close to the body. Allow enough space for feet to get under tables and conveyor belts. Provide clear access to shelves and adequate space around pallets. Reduce height differences during load travel. Keep loads between knuckle and shoulder height from origin to destination. Slide objects rather than lifting and lowering them.
Provide adjustable chairs for all operations. Chairs should swivel for side-lifting, whether they are located in the company president‘s office or on the small-parts assembly line.
Load Guidance
Some specific considerations when handling loads would include:
2 Elements of a Material Handling Ergonomics Program
2.1 Analyse management operations
We must first identify those materials handling is often one of the largest cost constituents of a product, operation or service. Needless handling of materials costs time and money.
We must understand the connection between workstation design and the works, that workers are expected to complete. The People responsible for planning work methods must pay particular consideration to details of the task involved to ensure the greatest possible synchronisation between the work method and the worker.
Make purchasing managers an important part of the materials handling program. Have them pay attention to details, such as size, weight, packaging and ease for handling. Use sold to/ship to arrangements to exclude in-plant handling wherever possible. Products being sent to your company for distribution may be more efficiently conveyed from your supplier to the customer, saving freight and handling. Reduce overall work-in-process quantities. Failure to do so often result in excess problems— extra handling, use of larger containers or parts piled. Housekeeping problems may grow, increasing possibilities of materials handling vehicle mishaps and damage to materials and completed goods. To reduce work-inprocess quantities, it is necessary to tighten up controls and shorten estimating for inventory, scheduling, ordering and shipping. Manufacturing products on an as ordered basis, instead of storing for anticipated use.
Perform product study. Alterations in the product sometimes result in decreased materials handling. Consider assuaging the product, and allowing a worker or conveyor to handle more pieces at one time. Plan to expand or change. Production usually suffers under packed conditions. Much of this material is reliant upon administration‘s policies and processes.
But even in the absence of management analysis, you personally can analyse and implement change in the following ways. Establish discarding and storage methods, and ways to progress material flow for scrap, waste materials, containers, tools and equipment. Each workstation must be analysed.
2.2 Material flow
It is usually not enough to simply observe and study a specific manual materials handling task. The key questions arise with respect to how the material is routed through the facility or work site that can only be answered by looking at the bigger picture.
Eliminate unnecessary materials handling by combining operations or shortening the distances that the materials must be moved. Look for crossing paths, loops, backtracking and a lack of direction during production. One benefit of short distances is the ability to link workstations by conveyors and reduce carrying distances. Also, less mechanical handling can mean fewer opportunities for forklift accidents. Walk through your operations with an employee. Make immediate simple changes. (Make written suggestions for observed cost-saving and people-saving changes that need approval or further evaluation.)
Take back to first principles, rearrange or change the process. Often, processes that are handled otherwise can be performed in a similar fashion to simplify the material flow. Plan an adequate aisleways for intended material flow, and emergency access and exit.
Employees must be able to evacuate quickly in an emergency. Small aisleways may restrict exits and cause panic. Emergency vehicles also must be able to quickly gain entrance. Adequate aisleways and exits facilitate the orderly movement of materials. Avoid the necessity of working in aisleways.
2.3 Workplace
Check the floor surfaces, repair flaws, depressions, holes, spoiled flooring and surfaces. Starting forces for carts can double or triple on poor surfaces. Worn-out or damaged wheels also can increase the required force. Insist on good housekeeping. Keep floor surfaces clean. Water, oil, grease and material scrap reduce traction and increase the force required to push or pull carts. Poor housekeeping only increases materials handling obstacles. Review plant design to remove building obstructions that interfere with materials handling.
In materials handling, “what goes down must come up.” To avoid repeated stooping and twisting, the goal is to bring both incoming and outgoing materials at each process to a suitable work height. We recommend at least a minimum of 20 inches above the floor, but ideally to knuckle height of about 30 inches. Reduce the need to raise or lower materials from above shoulder height. If you must raise or lower materials above shoulder height, store lighter objects on top shelves.
Remove constraints that prevent materials from being positioned close to the body. Allow enough space for feet to get under tables and conveyor belts. Provide clear access to shelves and adequate space around pallets. Reduce height differences during load travel. Keep loads between knuckle and shoulder height from origin to destination. Slide objects rather than lifting and lowering them.
Provide adjustable chairs for all operations. Chairs should swivel for side-lifting, whether they are located in the company president‘s office or on the small-parts assembly line.
Load Guidance
Some specific considerations when handling loads would include:
- Small is better than big.
Generally speaking, when it comes to the manual handling of loads, small is better than big. Large, stroppy loads present the handler with a variety of potential problems including added stress and strain to the upper extremities and the back. Containers should not be so high that they obstruct vision or, conversely, bump frustratingly against the legs as they are carried. Loads that will be lifted should be packed in containers slender enough to fit between the knees during a squat lift (knees and hips bent, and the back more or less straight). This design will allow the load to be placed close to the spine, thereby reducing the load‘s compressive forces on the spine.
- Loads should not be too light.
Loads that are too light may boost the handler to lift a number of units at a time, creating an unbalanced load that is more likely to fall. Contrariwise, loads should sometimes be made so heavy that individuals will not attempt to lift the load without the help of another somebody or will get mechanical assistance. Whenever possible, packages should be categorised with the content‘s weight so people who handle them will immediately know how heavy a load they are dealing with.
- Containers should be designed to prevent their contents from shifting.
Lots that shift in their containers may move the centre of gravity away from the handler, swiftly and traumatically increasing the load on the lower back. Similarly, loads that are unevenly spread in their container (a no symmetriccentre of gravity) place torsion on the spine. Therefore, it is suggested that packaging “capture” the contained items, to prevent movement within the container and hold the items in as symmetricpositioning as possible. For non-symmetric loads, the heavier portion of the container should be closest to the handler in order to keep the centre of gravity as close to the spine as possible.
- Boxes, totes, and containers should have handles.
Grips or hand cut-outs provide the best coupling between the handler and the object. According to the 1991 Revised NIOSH Lifting Equation, the ideal handle design is 0.75"–1.5" in diameter, at least 4.5" long, and features a 2.0" hand clearance. Handlers should be of a tubular shape with a smooth, nonslip surface. The optimal handhold cut-out has a 1.5" or greater height, a length of at least 4.5", a semi oval shape, and a 2.0" hand clearance, a smooth nonslip surface, and at least a 0.25" wall thickness. Supports near the bottom of the container allow the handler to carry the load near knuckle height and minimize static muscle loading of the upper extremities. The edges of the container should be smoothed, not sharp. Sharp edges create chances for contact stress between the box and the hand, arm and body.
Prioritize task analysis
Once we know material flow, it is time to evaluate tasks. This should be done on aimportance basis, first investigating the worst and most strenuous tasks. The safety and health unit should review accident statistics to determine priorities. The personnel who perform the tasks being evaluated are a vital source of information. Ask employees for their views on where the most vigorous, demanding and dangerous materials handling tasks exist likewise the poll supervisors and other management personnel. This is the time to examine the accident-investigation procedure to see if it is effective.
2.5 Analyse the job — tasks
Once the priorities have been set, break the tasks down into elements, which are the basic single actions needed to define the procedure at a particular stage of an operation. Among the considerations are:
- Identify manual materials handling is more than just lifting. It also includes dropping, pushing, pulling, and holding, carrying and transferring activities.
- Measure the occurrence and duration of the task. Determine the frequency of the task in activities-per-minute. Be sure to note how the activity fluctuates.
Lessen reach requirements. Design the operation to house the smallest person‘s reach. Avoid needless material stacking, storing or placement for work-in-process material (such as neatly orienting parts in containers when they will be dumped out in the next operation). Structure the equipment to use gravity to move materials wherever achievable. Simplify tasks by combining operations and steps.
2.6 Analyse the job — load
The load consists of the item or collection of items handled, many of which are stored in containers.
Adjust all containers for the required sizes. Use large containers for high-flow volume and small containers for low capacity. Avoid using large containers for low-volume materials to reduce the need for workers to reach.
Remove handling hesitations. Remove an employee‘s doubt about whether he or she should manually or mechanically handle an object by using obviously small and large containers or parts. The plot for incoming materials to arrive in suitable containers minimizes product handling.
Ask clients how you can best design product-needs packaging to meet their materials supervision needs.
Reduce deadweight ratio of containers. Consider the weight of the container which must be frequently handled and transferred vs. the parts inside. The weight of the container should be least compared to the weight of the product. Keep physically handled loads as small as possible, paying consideration to the width and length. To prevent blocked vision, load height should be 30 inches or less when manually carried.
The load centre of gravity (or balancing point) should be as close as possible to the person handling it. Stress on the back increases as the distance from your centre of gravity increases. For example, a 10-pound dictionary held 30 inches away from the body‘s centre of gravity would be the equivalent of a compact 50-pound load held close to the body.
Ensure that the load will be easy to grip. This can be done by ordering cardboard boxes with handle cut-outs; using ampoules with handles, lift straps or textured containers; and avoiding awkwardly designed items. Stabilize contents in boxes and containers to reduce surprises. Insert vertical baffles or dividers, balancing the weight in a box or using packing materials to avoid shifting parts. Minimize the potential for injury by caring the employee from loads with sharp edges or projections. Potential for injury also exists with reactive loads, such as metal shavings.
2.7 Equipment
Consider the use of mechanical aids whenever possible to assist employees in their materials-handling needs. Examples include:
- Pallet jack;
- Lift table;
- Two-wheeled hand truck;
- Lift and tilt table;
- Four-wheeled cart;
- Winch;
- Motorized hand truck;
- Manipulator;
- Hoist;
- Positioner;
- Crane;
- Up ender;
- Conveyor;
- Dumper;
- Chute;
- Powered industrial vehicle.
This includes, but is not limited to, identifying:
- What will be carried (assessing size, weight, and other pertinent parameters?)
- Overall weight and size capacity demands (using worst case load weight and size estimates)
- The terrain and anticipated travel path (identifying the presence of ramps, severe floor Irregularities, steps, or other obstacles)
- Pertinent environmental conditions (extremes in temperature, water, or chemical exposures, etc.)
- How frequently the unit will be used (infrequently to constantly)
- Information relating to the people who will use the device (user population characteristics versus load and device characteristics), as necessary and apt Such detailed information will help ensure that the indicated device will fit the task requirements, reduce ergonomic risk factors, and reduce the human burden. Wrongly designed or specified material handling aids have the potential to slow down work, lead the user to abandon the unit, or, worse, result in damage to the handler and perhaps to others. Choosing the right equipment can make work less bodily taxing, reduce material handling risk factors, and make performing the task more acceptable to a wider range of people.
There is a host of material handling skills available, including cranes, hoists, and monorails for lifting, lowering, and transporting; manipulators for picking and orienting; and work positioners and lift tables for lifting, lowering, and rotating objects. Carts, dollies, and trucks are used for moving loads, and a wide range of tools and equipment, intended to reduce physical stress associated with manual handling tasks, are available. Examples are conveyors, totes, flow racks, and ball transfers. Often teaming a blend of handling devices to work in concert as a system is desirable and should be considered. An example of this would be the use of a lift table used in conjunction with a conveyor and ball transfer to move materials from aacceptance department through an incoming scrutiny process area.
Bring only sufficient material to complete the job in the immediate work area. Extra material will either need extra handling to get it back to storage or will create overcrowding. Likewise, too little will require extra handling.
Consider the following, whenever possible, in jobs with considerable manual materials handling:
- Rotate employees from less strenuous jobs;
- Split work among two or more employees;
- Introduce appropriate work/rest schedules.
- Using mechanical handling aids. Workers may avoid mechanical aids because they simply do not know how to use them;
- Knowing materials handling problems in the workplace;
- Identifying actions that can prevent excessive manual materials handling;
- Proper body mechanics.
2.8 Environment
Review work areas for proper lighting levels. Poor lighting can cause accidents and injuries, and lessen quality of products.
Make allowances for weather situations including the following:
- Issue appropriate clothing, including gloves;
- Take measures to prevent cold and heat stress;
- Maintain aisles;
- Shield storage areas from mud and snow.
2.9 Recommend, review and implement changes
Once workers, staff and line employees have identified problems, they must be operated upon. At this point, shortages have been identified with possible answers in mind. The process is broken down into the following stages:
- Prioritize — Priorities are considered by the degree of hazard and risk associated with materials handling. These are determined as part of the initial organisation analysis of thematerials handling process, basically a historical approach. Risk is based on the frequency of worker contact to the hazards of any given task and the number of workers routinely exposed.
Two key elements of the review process are determining the influence proposed changes will have on other jobs, and what new difficulties will arise as a consequence of the changes made. Failure to consider these elements can result in a loss of credibility for the newly highlighted materials handling process.
3. Material Handling Ergonomics for human-beings
3.1 Lifting Principles
Maintain a neutral spine, keep your back straight!
Hold your abdominal muscles tight, but don’t hold your breath!
Use your legs to lift, not your back
Don’t bend over to lift
No twisting- move your feet instead
Maintain the load as close to your body as possible
3.2 Lifting Assistance
Seek assistance when lifting:
- Any loads >50 pounds (or any heavy load you do not feel confident lifting)
- Any large or bulky loads
- Any loads that are oddly shaped and difficult to handle
- Verbal Communication is important
- Designate a lift leader to ensure you: Lift at the same time
Walk in step
Lower the load together
Scan the environment for potential hazards first
- Whenever possible, use mechanical assistance (fork lift, hand truck, dolly) which will reduce the strain on your back over time.
- Maintain a neutral spine, keep your back straight!
- Hold your abdominal muscles tight, but don’t hold your breath!
- Use your legs to push or pull, not your back
- Don’t bend over when pushing or pulling
- No twisting- move your feet instead
- Maintain the load as close to your body as possible
- Remember: It is always safer and easier to push rather than pull
- Hold your abdominal muscles tight, but don‘t hold your breath!
- Balance the carried load right to left to prevent excessive strain on your spine.
- Whenever possible, utilize a cart to transport tools and equipment rather than lifting and carrying.
Published date : 31 Jan 2015 03:00PM