Indian students turn PPE waste into eco-friendly bricks without cement
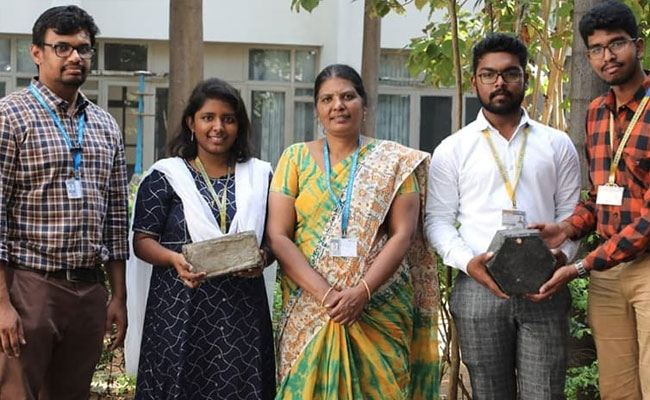
Not only do these "poly bricks" have a three-time higher compressive strength as compared to the common red bricks, they are much lighter and can be produced in a far shorter time.
Since the curing time to reach ISO standards is less than 24 hours, the bricks are ready quicker and cheaper than common red or concrete hollow bricks and meet the water absorption specifications.
The team from the civil engineering department of Sona College -- Aravind Kumar from final year, Kamalesh J B and Dharani Raj U, both from third year, and Adhavan P and Harshini E K, both from second year -- found this solution while participating in a nation-wide competition.
"The technology is now available to hospital chains and other organisations interested in technology transfer to help tackle PPE waste and also reduce poisonous emissions," Chocko Valliappa, Vice Chairman, Sona Group of education institutions, told IANS.
The poly brick making process starts by sterilising PPE kits with ultraviolet (UV) rays, subjecting it to heat at 160 degrees centigrade, adding sand aggregates and casting the polypropylene mass into bricks.
The poly bricks are eco-friendly as they do not use any cement or water in the process and cause minimal in process emissions as the PPE plastic waste is subjected to less than 200 degrees centigrade.
The WHO recently said the use of PPE kits used during the Covid-19 pandemic was putting on the environment, due to their single-use nature.
According to the educational institution, these eco-friendly bricks can be used as regular bricks for walls as also as paver blocks instead of red bricks -- in the process reducing plastic waste as well as pollution caused during cement production.
The poly bricks have good cement adhesion and can be plastered with cement.
Dr N Karuppasamy, Assistant Professor of Civil Engineering, Sona College of Technology who mentored the team said that a patent application has been filed for this technology.
The civil engineering department has also patented a technology to use plastic waste in brick production that replaces almost 70 per cent of sand with plastic.